What Does PTA (Projected Time of Availability) Mean?
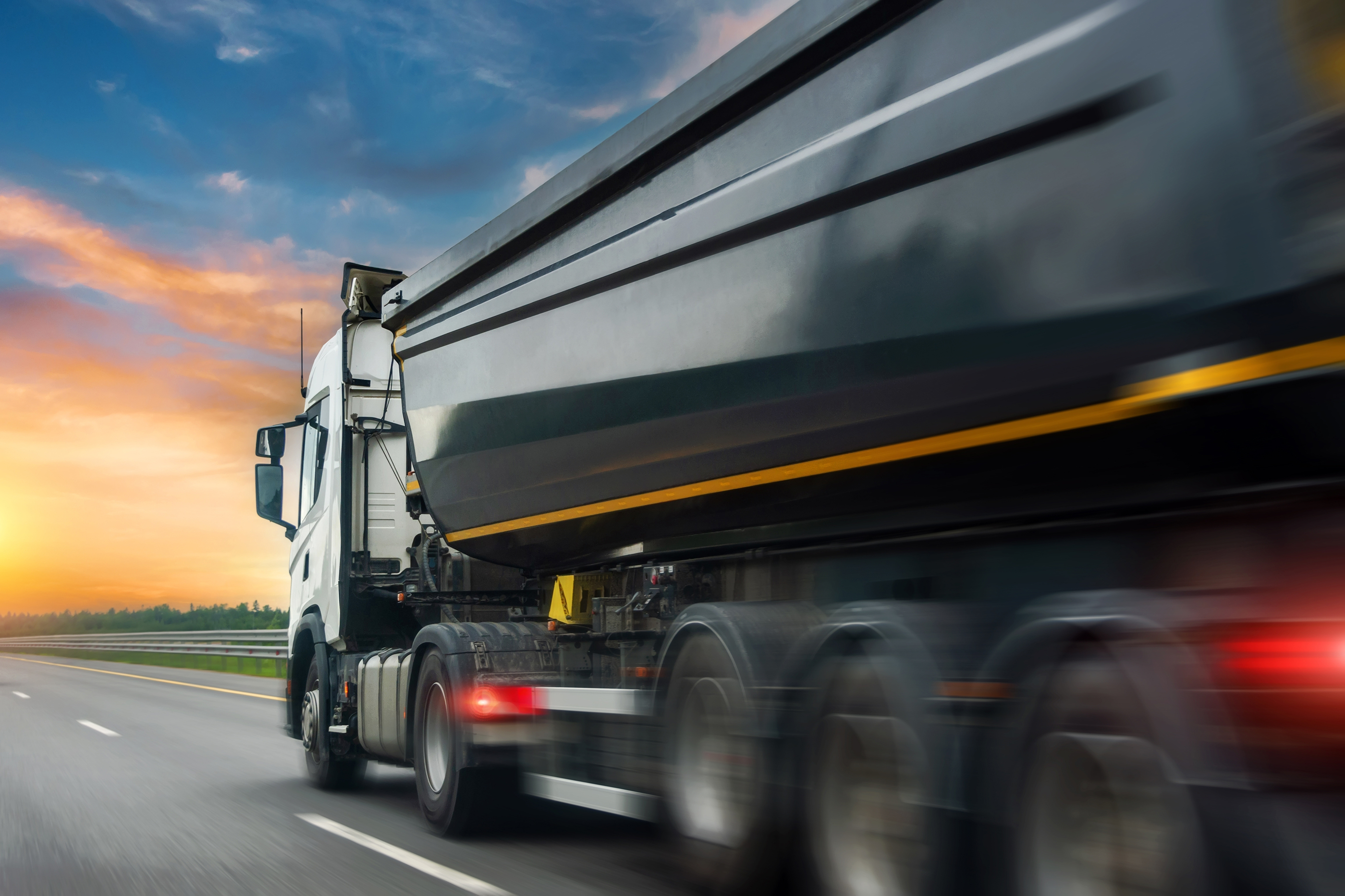
Projected time of availability—a critical factor in the trucking industry— affects many aspects of fleet operations. Not only does it have a direct impact on the efficiency and effectiveness of transportation operations, it also can be critical in meeting customer expectations, reducing costs, and helping carriers maintain a competitive edge in a dynamic and time-sensitive sector. So, what is projected time of availability?
What is projected time of availability?
In the context of trucking and logistics, PTA refers to the estimated time at which a particular resource, such as a truck or a shipment, will become available for use or delivery. This term is commonly used in coordination and scheduling aspects in the transportation industry.
For example, if a truck is currently engaged in a delivery, or is at a specific location for loading or unloading, the projected time of availability would indicate when it is expected to be free and available for the next delivery or assignment. This PTA information is crucial for efficient route planning, resource allocation, and coordination within logistics.
Other factors that influence the projected time of availability include time required for loading and unloading, travel time between locations, potential delays due to traffic, adverse weather, or other unforeseen circumstances, and the overall scheduling of transportation tasks.
What is PTA in dispatching?
PTA plays a pivotal role in streamlining operations for trucking dispatchers by providing them with timely and accurate information upon which to make informed decisions, optimize resources, enhance customer satisfaction, and improve overall efficiency in the transportation process.
- By utilizing precision route planning tools for PTA, dispatchers can:
- Monitor real-time location and progress of vehicles
- Communicate effectively with drivers
- Use dynamic routing based on weather or traffic conditions
- Set up automated alerts and notifications if deviations seem imminent
- Update customers with more accurate information to manage expectations
- Examine historical PTA data to identify patterns and trends
- Establish new training protocols for drivers who are experiencing delays because of certain behaviors
- Align hours of service with the valuable PTA data
ETA vs. PTA meaning in trucking
ETA (estimated time of arrival) and PTA are both acronyms used in the context of time estimates, especially in transportation and logistics, but they represent different concepts:
ETA - Estimated Time of Arrival:
- Meaning: ETA refers to the anticipated or estimated time at which a vehicle, shipment, or person is expected to arrive at a specific destination.
- Application: In the context of transport, ETA is commonly used to provide an estimate of when a vehicle (such as a truck or service vehicle) is expected to reach a particular location.
PTA - Projected Time of Availability:
- Meaning: PTA, on the other hand, refers to the estimated time at which a particular resource, such as a truck or a shipment, will become available for use for the next delivery.
- Application: PTA is often used in logistics and transportation management to plan and coordinate activities, indicating when a resource will be free to take on other tasks.
In summary, ETA is primarily concerned with when a fleet vehicle or delivery will reach a destination, while PTA focuses on when a resource will become available for use in the next task in the transportation or logistics process.
Both concepts are crucial for effective planning, scheduling, and coordination in various industries, including trucking and transportation.
10 critical areas where PTA in trucking can make all the difference
- Resource optimization: Knowing the availability of trucks and other resources allows for better planning and optimization of transportation routes. This helps in reducing idle time and maximizing the utilization of assets, ultimately improving cost-effectiveness.
- Timely deliveries: Availability plays a pivotal role in meeting delivery deadlines. Timely and accurate information about when trucks will be available enables logistics professionals to schedule deliveries efficiently, ensuring that goods reach their destinations on time.
- Customer satisfaction: Reliable and predictable transportation services contribute to customer satisfaction. Knowing when trucks are available allows for accurate communication of delivery schedules to customers, helping build trust and maintain positive relationships.
- Reducing downtime: Minimizing downtime is crucial in the trucking industry. By having a clear understanding of when trucks will be available for the next assignment, companies can reduce waiting times, avoid unnecessary delays, and keep the transportation network operating smoothly.
- Route planning for PTA: Availability information aids in strategic planning and decision-making. Logistics managers can allocate resources effectively, plan for maintenance schedules, and adjust routes based on the projected availability of trucks, thus leading to better overall operational efficiency.
- Cost efficiency: Efficient utilization of resources translates into cost savings. By minimizing idle time and optimizing routes, trucking companies can reduce fuel consumption, maintenance costs, and other operational expenses.
- Compliance with regulations: Availability information is essential for complying with regulatory requirements. Knowing when drivers and trucks will be available helps in adhering to legal restrictions on driving hours and rest periods, ensuring compliance with safety regulations.
- Adaptability to changes: The trucking industry often faces unforeseen challenges such as traffic congestion, weather disruptions, or unexpected delays. Knowing the availability of resources allows for quick adaptation to these changes, minimizing the impact on schedules and deliveries.
- Improving driver satisfaction: When a driver is under pressure to perform a set of deliveries/tasks on constrained timelines, it can dramatically affect morale and even cause the driver to break traffic laws to meet impossible deadlines. By better understanding—and being able to meet projected timelines based on data, the pressure to create unreasonable delivery schedules is greatly diminished.
- Motoring public safety: By ensuring drivers have sufficient rest and comply with hours of service (HOS) regulations, PTAs contribute to improved safety on the roads.
How to improve PTA in trucking
Trucking fleets can enhance their projected time of availability (PTA) and overall timelines through the implementation of various strategies and technologies. Here are several ways in which trucking fleets can improve their efficiency:
- Route optimization software: Utilize advanced route optimization software to plan the most efficient and time-effective routes. These tools consider factors such as traffic, weather, and road conditions to minimize travel time.
- Real-time fleet tracking and visibility: Implement GPS tracking systems and real-time visibility solutions to monitor the location and status of vehicles. This allows for better management of resources and timely interventions in case of unexpected delays.
- Telematics technology: Invest in telematics technology to gather and analyze data on vehicle performance, driver behavior, and fuel efficiency. This information can be used to optimize routes and improve overall fleet productivity.
- Predictive analytics: Leverage predictive analytics to anticipate potential delays and proactively address issues before they impact timelines. Analyzing historical data can help in making more informed decisions about routes and scheduling.
- Dynamic scheduling: Implement dynamic scheduling systems that can adjust in real-time based on changing conditions. This flexibility helps in adapting to unexpected events and maintaining overall efficiency.
- Collaboration and communication: Foster effective communication and collaboration among drivers, dispatchers, and other stakeholders. Clear communication channels enable quick responses to changing situations and ensure everyone is on the same page.
- Maintenance planning: Develop proactive maintenance schedules to minimize breakdowns and unexpected downtime. Regular maintenance checks can prevent issues that might otherwise disrupt timelines.
- Driver training and education: Provide ongoing training for drivers on efficient driving techniques, compliance with regulations, and the use of technology tools. Well-trained drivers are more likely to contribute to the overall efficiency of the fleet.
- Load planning and optimization: Optimize load planning to ensure that trucks are carrying optimal loads while adhering to weight limits. Efficient load planning contributes to fuel efficiency and overall fleet productivity.
- Data integration: Integrate data from various sources within the fleet, including logistics, maintenance, and operations. A unified data approach allows for better analysis and decision-making to improve overall efficiency.
- Continuous improvement culture: Foster a culture of continuous improvement within the fleet. Regularly review processes, seek feedback from drivers and staff, and implement changes to address any identified inefficiencies.
By adopting a combination of these strategies and leveraging technology for PTA in trucking, fleets can enhance their projected time of availability and more accurately buildout timelines, thus leading to improved overall efficiency and customer satisfaction.
Learn more
To learn more about how Lytx® technology can help you better fine-tune PTA for your transport vehicles, contact us or book a demo today!