Tri-Axle Trucks: Safety and Compliance Considerations
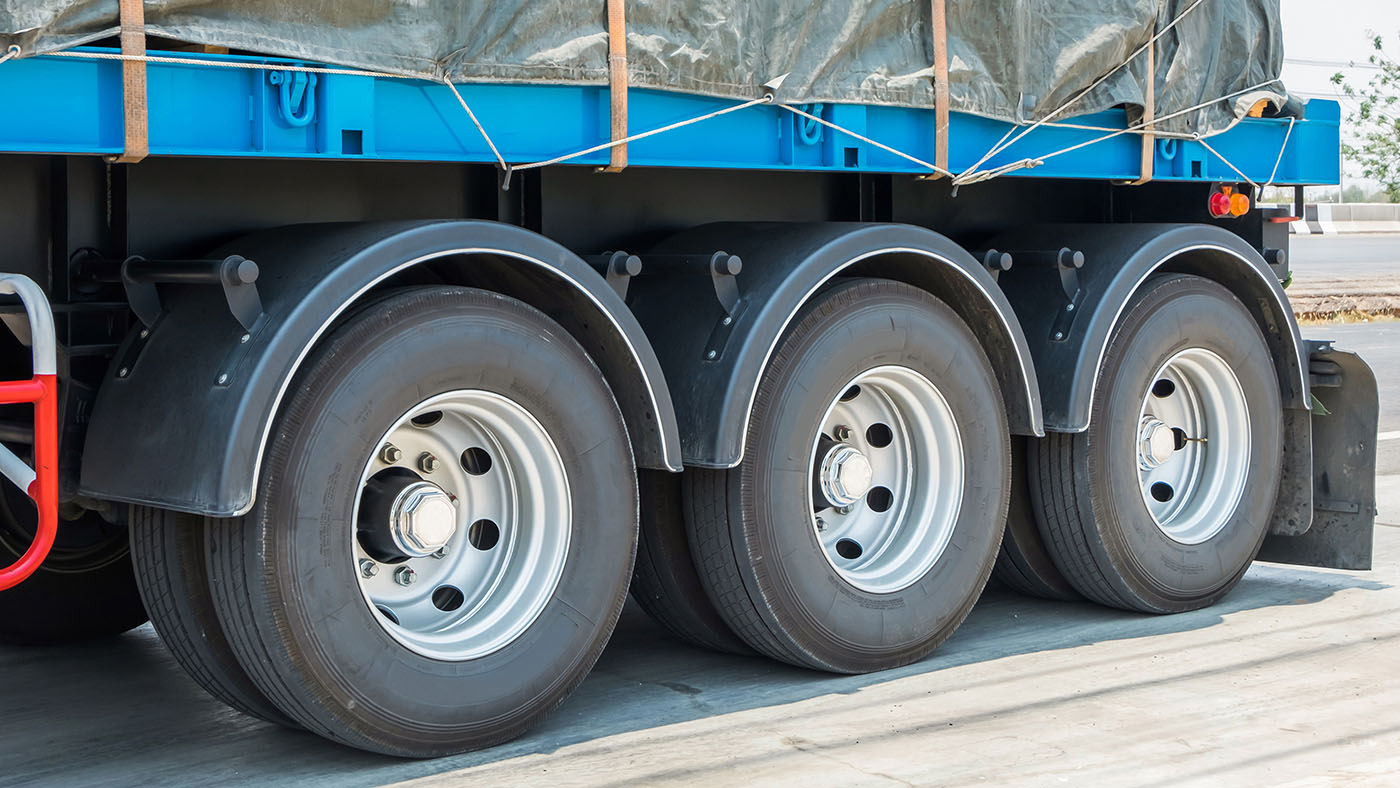
In the world of trucking and shipping, different types of transport operations call for different types of vehicles. While vans and container trucks are typically used for last-mile delivery, there are other categories of vehicles, including tri-axle trucks/trailers (also known as a triple axle truck), often used for both short- or long-distance hauling when the cargo being transported exceeds a certain weight.
What is a tri-axle truck?
A tri-axle truck is a type of commercial truck that has three axles, or sets of wheels, in the rear. Companies with three-axle truck fleets commonly use them for transporting heavy loads over long distances, and in industries such as construction, large-capacity shipping, and logistics. The additional axle provides extra support and weight-bearing capacity, allowing the truck to carry heavier loads than a standard two-axle truck.
Tri-axle trucks play a crucial role in the transportation of goods and materials, particularly in industries where heavy loads are common.
Types of tri-axle trucks
Tri-axle configurations are found in various types of trucks, including dump trucks, tri-axle tractor-trailers, and concrete mixers.
Tri-axle dump trucks, for example, are commonly used in construction for hauling materials like gravel, sand, or dirt. Larger and more powerful than standard dump trucks, triple axle dump trucks carry heavier loads over longer distances. The hydraulic dump bed, key feature, allows for efficient unloading of materials at the job site.
The capacity of a triple axle dump truck varies depending on the make and model of the vehicle. Generally speaking, most tri axle dump trucks are capable of carrying between 25 and 30 tons of material. However, the capacity of a dump truck can be affected by factors such as the weight distribution of the load and the condition of the roads to be traveled.
Key features and characteristics of tri-axle trucks
Axle configuration
The tri-axle configuration typically consists of two drive axles and one non-driving axle in the rear. The additional axle helps distribute the weight more evenly, reducing the impact on each individual axle and complying with weight regulations.
Payload capacity
Tri-axle fleet trucks are designed to carry heavier loads compared to two-axle trucks.The increased weight-bearing capacity is advantageous for transporting bulk goods, construction materials, and other heavy items.
Stability and control
The extra axle enhances stability and control, especially when the truck is fully loaded. This stability is important for safety during transportation, especially on highways and uneven terrain.
Regulatory compliance
Tri-axle fleet trucks are often used to comply with weight regulations imposed by transportation authorities. These regulations aim to prevent excessive wear on roads and bridges caused by overweight vehicles.
Cost and fuel efficiency
While tri-axle trucks offer advantages in terms of weight distribution and capacity, they may have higher upfront costs compared to two-axle trucks. Fuel efficiency can be affected by the additional weight, but advancements in technology aim to mitigate this impact.
Tri-Axle trailer suspension
The suspension system on tri-axle trailers is crucial for ensuring stability, load-bearing capacity, and a smooth ride. The suspension components work together to absorb shocks and vibrations, distribute weight evenly, and provide support for the trailer and its cargo. Here are some common types of tri-axle trailer suspensions:
Leaf spring suspension
Leaf spring suspension is a traditional and widely used system for tri-axle trailers. It consists of multiple layers of flexible metal strips (leaf springs) attached to the trailer's axles. The springs absorb shocks and help distribute weight.
Air suspension
Air suspension systems use airbags to provide support and dampening. These airbags can be adjusted to maintain a consistent ride height and accommodate varying loads. Air suspension is often preferred for its adjustability and ability to provide a smoother ride.
Torsion axle suspension
Torsion axles use a rubberized torsion bar inside the axle tube to provide suspension and support. This type of suspension is known for its durability, simple design, and ease of maintenance.
Independent suspension
Some high-end or specialty tri-axle trailers may use independent suspension systems, where each wheel has its own suspension components. This allows for better handling, especially on uneven terrain, but it can be more complex and expensive.
Walking beam suspension
Walking beam suspension consists of a pivoting beam that connects the axles. As the trailer encounters uneven terrain, the beam allows the axles to move independently, providing better traction and stability.
Slipper spring suspension
Slipper spring suspension uses a single leaf spring that slips over a hanger at one end, while the other end is fixed to the trailer. This design simplifies the suspension system and is commonly used in light to medium-duty trailers.
Rubber torsion axle suspension
Rubber torsion axle suspension uses rubber cords inside the axle tube to provide suspension and dampening. This type of suspension is known for its smooth ride and low maintenance.
When choosing suspension for tri-axle trailers, factors such as the type of cargo, the intended use of the trailer, road conditions, and regulatory requirements must be considered.
Regular maintenance and inspections of the suspension system are crucial to ensure optimal performance and safety. Refer to each trailer’s manufacturer and suspension system suppliers for additional information on specifications and guidelines for proper use and maintenance.
How many tons does a tri-axle truck safely hold?
While legal axle weight limits for commercial trucks vary, with rules for fleet transport vehicles requiring tri-axle trucks carry no more than 34,000 pounds (around 15 tons), there is some variation depending on the size of the trailer being pulled, its contents, and the materials used in the trailer’s construction.
General highway rules dictate that single axle trucks can carry no more than 20,000 pounds, but the total weight allowed any semi-trailer can pull in North America cannot exceed 80,000 pounds, which includes gross vehicle weight.
In terms of tonnage, there are gray areas that depend on several factors. For a tri-axle fleet truck (meaning three axles on the truck itself), the weight distribution across these axles is crucial. Weight limits are often set for each axle or axle group to prevent excessive stress on roads and bridges. The weight carried by each axle or axle group needs to comply with both federal and state regulations.
It's important to note that weight limits can vary by country, state, and even local jurisdiction. Additionally, there may be specific regulations for certain types of cargo, such as hazardous materials or oversized loads.
To determine the maximum weight a specific tri-axle vehicle can legally transport in a given area, consult the relevant local transportation authorities or regulations. Truck operators must adhere to these regulations to ensure road safety, prevent damage to infrastructure, and comply with the law. Overloaded vehicles can pose safety risks, contribute to wear and tear on roads and bridges, and result in costly fines for tri-axle fleet companies who do not comply with regulations.
Two-axle vs. tri-axle vs. quad-axle: what’s the difference?
The primary difference between a two-axle, tri-axle, and a quad-axle vehicle lies in the number of axles and wheels. While all configurations are commonly used in the trucking industry, tri and quad-axle vehicles are typically used for transporting heavy loads. However, key differences lie in how the number of axles affects the vehicle's weight distribution and overall load-carrying capacity as well as maneuverability. The more axles a vehicle has, the less maneuverable it may be in tight spaces.
Load capacity
The quad-axle configuration generally allows for a higher payload capacity compared to a tri-axle. The additional axle helps distribute the weight more effectively, reducing the strain on individual axles and complying with weight regulations. Two-axle trucks differ as they typically transport lighter cargo loads as there are only two areas to distribute the weight being transported.
Stability
While configurations aim to provide stability, a quad-axle vehicle may offer slightly better stability due to the additional axle and the ability to distribute weight more evenly.
Regulatory compliance
Both tri-axle and quad-axle vehicles must comply with weight regulations imposed by transportation authorities. The number of axles and their spacing are critical factors in meeting these regulations. Some equipment, such as doubles and triples may also require special driver endorsements (such as a “T” endorsement) in addition to having a CDL.
Choosing between two-axle, tri-axle, or quad-axle depends on the specific requirements of the transportation task, including the weight of the cargo, road regulations, and the intended use of the vehicle. As always, truck operators must ensure that their vehicles adhere to local laws to ensure safe and legal operation.
What is a tag axle on a truck?
A tag axle, also known as a "booster axle," is an additional axle on a truck that is not powered by the engine. Unlike the drive axles, which receive power from the engine to move the truck, the tag axle is passive and does not contribute to the truck's propulsion. Instead, its primary purpose is to provide additional support for carrying heavier loads and improve weight distribution. Here are some key characteristics and functions of a tag axle on a truck:
Weight distribution
One of the primary functions of a tag axle is to distribute the weight of the truck and its load more evenly. This helps to comply with axle weight regulations and reduces the impact on individual axles, preventing excessive wear on roads and bridges.
Increased payload capacity
By adding a tag axle, the truck's overall weight-bearing capacity is increased. This is particularly beneficial when hauling heavy or oversized loads, allowing for the transportation of more cargo while maintaining compliance with weight regulations.
Improved stability
The additional axle contributes to improved stability, especially when the truck is fully loaded. This is important for safe and controlled operation, particularly during maneuvers and when driving on uneven terrain.
Adjustable or lift axles
Some tag axles are designed to be adjustable or "lift" axles. This means they can be raised when not needed, reducing tire wear and improving fuel efficiency. When additional support is required, such as when carrying a heavy load, the axle can be lowered to engage and provide support.
Steerable tag axles
In some configurations, tag axles may be steerable. Steerable tag axles can enhance maneuverability, especially in tight spaces or when navigating through urban areas.
13 Key safety considerations for tri-axle trucking companies
Safety is a top priority for tri-axle trucking companies to ensure the well-being of their drivers, the public, and the integrity of the cargo being transported. Here are some key tri-axle safety tips for safety for trucking companies:
Driver training
Ensure that drivers receive comprehensive training on the safe operation of tri-axle trucks. This includes proper loading and unloading procedures, weight distribution, and adherence to safety regulations. In addition to driver training, trucking companies need to make sure drivers have the appropriate class of CDL, either A or B, depending upon the equipment being driven.
Compliance with regulations
Stay informed about and comply with local, state, and federal regulations governing tri-axle trucks. This includes weight limits, axle spacing requirements, and any specific regulations related to the type of cargo being transported.
Regular maintenance
Implement a rigorous preventative maintenance schedule for all tri-axle trucks to ensure that they are in optimal working condition. Regular inspections should cover brakes, tires, lights, and other critical components.
Weight distribution
Properly distribute the weight of the cargo to avoid overloading specific axles. Weight imbalances can affect the vehicle's stability and handling, increasing the risk of accidents.
Route planning
Plan routes that take into account the condition of roads, bridges, and tunnels. Be aware of weight restrictions and any specific regulations along the planned route.
Driver fatigue management
Implement policies and practices to manage driver fatigue, such as limiting driving hours, providing rest breaks, and encouraging healthy sleep habits. Fatigue is a significant contributor to accidents as seen in statistics on drowsy driving.
Technology integration
Consider integrating fleet safety technologies, such as collision avoidance systems, lane departure warnings, and fatigue monitoring systems, to enhance overall safety.
Emergency response plans
Develop and communicate emergency response plans in the event of accidents, breakdowns, or hazardous material spills. Ensure drivers are trained on proper emergency procedures.
Load securement
Train drivers on proper load securement practices to prevent cargo from shifting during transit. This includes using appropriate tie-downs, straps, and other securement methods.
Communication and documentation
Foster clear communication between drivers, dispatchers, and other personnel. Maintain accurate documentation of driver vehicle inspections, maintenance records, and driver logs.
Weather conditions
Monitor seasonal weather conditions and advise drivers accordingly. Provide guidelines for safe driving in adverse weather, such as rain, snow, or high winds.
Continuous improvement
Establish a culture of continuous improvement regarding safety. Encourage feedback from drivers and use incidents or near-misses as learning opportunities to enhance safety protocols.
Safe stopping distance
Under normal road conditions, and at a speed not exceeding 55 miles per hour, the safe stopping distance for a tri-axle truck is approximately 400 feet. For a truck traveling at 65 miles per hour, that distance increases to 525 feet.
By prioritizing these safety considerations, tri-axle trucking companies can help reduce the risk of accidents, protect their personnel and assets, and contribute to overall road safety. Regular training, adherence to regulations, and a commitment to continuous improvement are key elements in building a strong safety culture within the company.
What are the triple trailer states?
As of January 2022, the use of triple trailers, also known as triple-doubles or turnpike doubles, is regulated by individual states in the United States. The specific regulations and permissions for triple trailers vary from state to state. Some states allow the use of triple trailers on certain roads and under specific conditions, while others prohibit or restrict them altogether.
Per this writing, the triple trailer states are:
Alaska | Arizona | Arkansas |
Colorado | Idaho | Indiana |
Kansas | Michigan | Minnesota |
Montana | Nebraska | Nevada |
New York | North Dakota | Ohio |
Oklahoma | Oregon | South Dakota |
Texas | Utah | Washington |
Wisconsin | Wyoming |
For the most accurate and up-to-date information, it is recommended to check with the relevant state transportation authorities or consult the state's official transportation regulations.
Final thoughts
If your fleet is contemplating using or already utilizing tri-axle vehicles there are a number of tools that can help you manage and protect your fleet. Lytx® has a variety of fleet management solutions to help keep your drivers safe and your vehicles healthy and compliant on the road.
To learn more, contact us or book a demo today.