Improving Construction Fleet Productivity and Efficiency
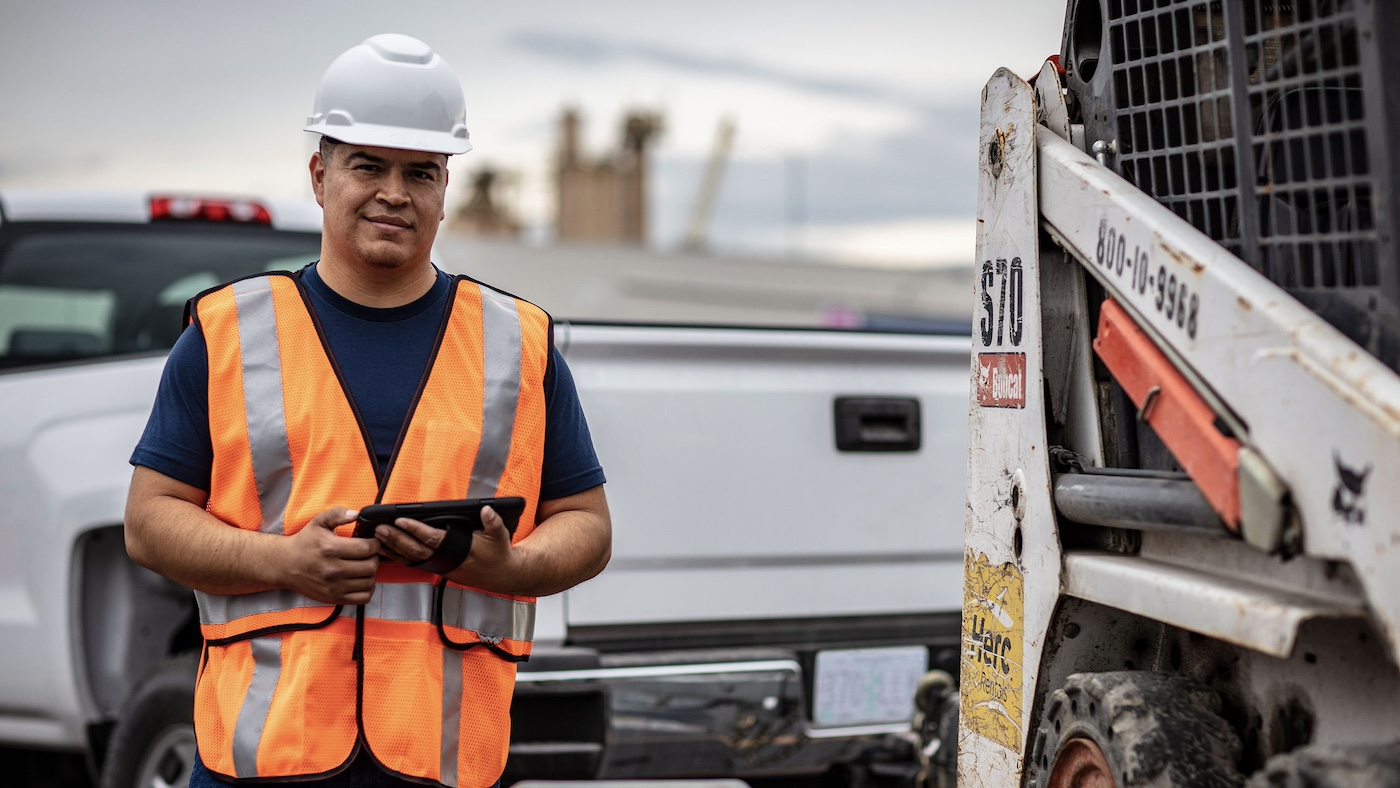
With the lingering economic effects of COVID combined with global disasters and conflicts arising over the last few years, material shortages and other challenges continue to hinder the construction industry. With that in mind, improving construction fleet productivity and efficiency without compromising safety is often top of mind for many construction fleet and operations managers.
One of the best ways to curb economic and other constraints is to keep projects on time and on budget. Meeting tight deadlines helps reduce costly overruns, helos avoid the necessity of new permits, and keeps upcoming projects from being derailed or pushed back. In addition, as reputation is important in acquiring new business, maintaining a safe track record and showcasing a proven history of efficiency in construction projects is invaluable to continued success.
How to improve fleet productivity in the construction industry
For fleet operations managers who are responsible for both drivers and vehicles from the time they leave the lot until they return, comprehensive fleet tracking software is one of the most powerful tools they can have in their arsenal.
Even better, adopting a solution that requires minimal hardware and onboarding time while providing a full array of solutions and reports. This can be a lifesaver for managers who need to focus on other important aspects of the business, including acquiring new customers, managing existing clients, creating budgets, hiring new drivers, and keeping fleets road ready.
While construction fleet tracking software provides a digital “roadmap” of all activities of a fleet, it can also help fleet managers create plans to address problems and give them important insights, including the following benefits.
1. Increased safety
With a fleet tracking solution, construction fleet managers can gain insights into how their drivers are performing behind the wheel. Using engine control module (ECM) data and other inputs, the software can help managers uncover whether drivers are tailgating, speeding, making abrupt stops, and more.
Combined with a video safety solution, video telematics can help provide a complete picture of risk, with the critical context needed to understand what really happened. Armed with this information, managers can help their drivers improve bad habits for a safer and more productive fleet.
2. Decreased fuel costs
As fuel costs skyrocket, a fleet tracking system can help construction fleet managers be aware of fuel-saving metrics, such as vehicle tire pressure, scheduled maintenance, misuse and abuse, brake-life, and more.
When you multiply the potential savings of improved driver behavior and vehicle maintenance across an entire fleet of construction vehicles, small changes can lead to significant savings. Managers can potentially see a dramatic reduction in monthly fuel expenditures over time.
3. Asset tracking
Equipment theft is a booming business with the potential to wreak havoc on an organization's bottom line and overall project success. Almost $1 billion in large machinery is lost or stolen in the United States every year, and 75 percent of it is never recovered.
Luckily, powered asset tracking can help fleet managers keep track of valuable equipment. Managers can check in on equipment location at any time, and enable notifications to alert them to any potential misuse or theft via geofencing.
4. Minimizing idle time and increasing labor efficiency
It may not seem like a costly metric, but idling time can be a major waster of fuel that many fleet managers are unaware of. The right telematics system will not only give managers insights on driver behaviors, but provide valuable information on vehicle engine diagnostics including how much time is spent idling.
Simple things such as idling reports can help managers encourage better operator behaviors for reduced costs and greater productivity. Even more, to establish idling guidelines so their drivers can fully reduce waste.
5. Optimizing vehicle utilization
Optimizing fleet utilization is an increasingly important way to curtail costs and improve construction productivity and efficiency. Fleet tracking data shines a spotlight on utilization metrics, helping executives decide whether to invest or divest in assets for a more profitable business.
For this managers can take the data that is gleaned from a variety of metrics and turn the information into a tangible plan that is explained to all stakeholders. By optimizing fleet utilization, managers can dramatically improve efficiency and return on investment (ROI) of capital, while also adding to the bottom line.
What to consider when looking for GPS fleet tracking software for construction fleets
Construction fleets looking for the right software for their construction fleet management needs can use the following suggestions as guidelines when vetting potential solutions.
Determine your business goals
The first step is to determine your business objectives. What are you hoping to accomplish with construction fleet tracking software? Some companies are simply looking for cost savings like cutting down on fuel and insurance expenditures, while others may be looking to increase the productivity of existing assets and more. Determining your business goals is step one in finding the solution that is right for your enterprise.
Gain cross-departmental alignment
Once you have established your goals, it’s important to gain buy-in from the entire company– from the C-suite to safety and operations. In order to be successful, implementing a new software solution will require all hands on deck to ensure a smooth transition. By establishing inter-departmental synergy, you create an atmosphere that’s ready for success.
Provide incentivized onboarding opportunities
Once your organization has decided on a solution, it's important to help team members feel empowered with comprehensive training and onboarding. Perhaps provide “lunch and learns” to incentive learning and to show everyone that they are valued and an integral part of the success of the company.
Explain the importance of compliance
Assure your employees that the addition of construction fleet tracking software is for their benefit to ultimately improve overall fleet safety and operations. If you notice strong resistance or hesitation, hcheck out our guide to learn more about how to get drivers to use dash cams.
What does success look like to your construction company?
Once implemented, you can work towards a common goal and provide monthly, quarterly, or biannual results that keep everyone engaged using predetermined metrics of success. Your specific targets are up to you, but here are some possible objectives:
- Improve fuel efficiency
- Reduce insurance costs
- Decrease collision frequency
- Improve on-time delivery schedules
- Educate and coach your drivers to help them eliminate unsafe behaviors
- Provide a video telematic solution for dispatchers & customer service to ensure customer response & efficiencies
- Create top-to-bottom best practices for your company
- Ensure ROI of invested or deployed vehicles or equipment (capital expenditures)
- Generate reports with accurate, real-time data that shows the true lay of the land and progress you can report to all employees
- Share reports with potential new clients to demonstrate operational efficiencies
Construction fleet tracking software from Lytx
Lytx® has an array of construction fleet management solutions to help you meet your business goals. Whether you’re looking to improve project timelines, fine-tune budgets, or simply create a more cohesive plan to help your fleet be more successful, we can help.
Contact us or book a demo today!