Are Your Fleet’s Inefficiencies Coming from Inside Your Company Culture?
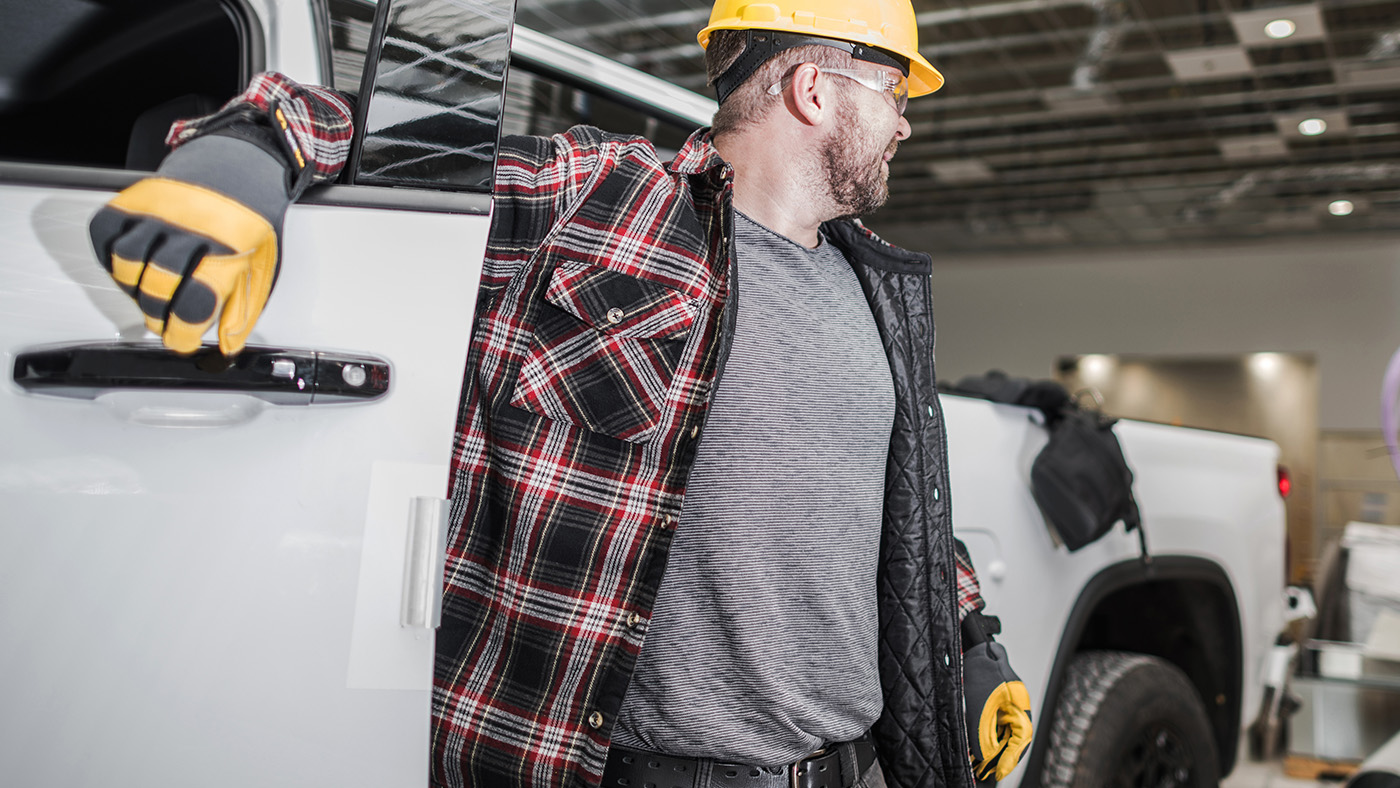
If your fleet is bogged down in inefficient practices, consider making safety your core cultural value.
In field services operations, efficiency is crucial, if elusive. Schedules change, customers are capricious, insurance premiums fluctuate, and technicians come and go.
In pursuing efficiency, companies will scrutinize every operational function for potential improvements, from maintenance and routing to fuel use. But this quest for efficiency often overlooks one important factor: company culture. Could your fleet's inefficiencies stem from a lack of internal emphasis on safety?
This blog explains how positioning safety as your core value can positively impact the efficiency of your field services operations.
Efficiency stands on the shoulders of safety
Many organizations address safety with strategies that are separate and distinct from operational efficiency.
But safety and efficiency are linked at every stage of fleet management:
Operations
Centering safety as a core cultural value fosters practices that prioritize the well-being of employees, customers, and the public at large. This translates into regular field technician safety training, meticulous vehicle maintenance schedules, and adherence to safety protocols. Consequently, breakdowns, injuries, and collisions occur more infrequently, allowing for uninterrupted operations and timely service calls. In addition, technicians who feel their company has their back tend to stay on the job longer, reducing employee turnover.
Maintenance
When safety is emphasized with proactive maintenance schedules and consistent, thorough inspections, mechanics are empowered to make inspections and repairs without cutting corners, and technicians know they are driving finely tuned vehicles. This proactive approach reduces downtime and prolongs the lifespan of fleet assets, ensuring that vehicles stay on the road and other machinery remains up and running.
Routing and fuel use
Efficient routing is not just about getting to a service call on time; it's also about minimizing risks and maximizing fuel efficiency along the way. A safety-focused company culture uses advanced route planning that, when possible, steers clear of traffic, hazardous weather, and road conditions that can add needless technician stress or fatigue. Efficient routing also means deploying the closest, most qualified technician to a job, which increases customer satisfaction while reducing technician time on the road. As a result, not only are deliveries and service calls made promptly, but vehicle wear and tear is minimized.
A safety culture’s positive effect on the bottom line
A safety-centric culture exerts a profound influence on costs, leading to savings across various aspects of field services fleet management.
Insurance premiums
Insurance companies reward proactive risk management practices. By demonstrating a commitment to safety through ongoing training, detailed maintenance records, and safety technology investments that have been proven to reduce collisions and risk, fleets can negotiate lower premiums and reap better coverage terms.
Claims and liabilities
A company culture that centers safety as a core value translates to better field technician driving skills, resulting in fewer incidents and lower claims costs. In addition, when a company embraces the use of safety technologies, such as video safety and video telematics systems, fleets can mitigate risks and avoid potential liabilities.
Regulatory compliance
Non-compliance with safety regulations can mean hefty fines. Leading with safety encourages adherence to regulatory requirements, avoiding costly penalties.
Brand and reputation
Catastrophic incidents and chronic roadway breakdowns pose a threat to a well-built brand. Reputation is hard to earn and easy to lose.
Steps to building a strong safety culture In pursuit of efficiency, lean into safety. Here are some steps toward cultivating a safety culture within your operations:
Get buy-in at the top
Company culture starts with the leadership team, who establish the clear moral imperatives for the organization. With leaders on board, managers can effectively roll out and reinforce safety initiatives in phases, with each success leading to more efficiencies across your organization.
Ask questions and establish goals
Within this phased approach, ask questions that can help establish goals and create consensus on how to reach them: What change do you hope to bring about by centering on safety? What does this change look like? Who are your internal safety ambassadors? What are the roadblocks, and how will progress be measured? Also, think about the best time to initiate change.
Bring technicians and other team members on board
Investing your technicians in a culture of safety means empowering and incentivizing them to make positive changes toward overall goals. Encourage a culture of open communication and consensus building, where positive intent is assumed, incidents are analyzed for root causes, and processes are refined to prevent recurrence. Recognition for effort and performance goes a long way toward building and keeping momentum in the right direction.
Safety has no finish line. If you start with safety, organizational efficiency will follow. As efficiencies become evident, move goalposts in a thoughtful, achievable way. Remember that safety (and efficiency) is an ongoing, consistent effort every single day.